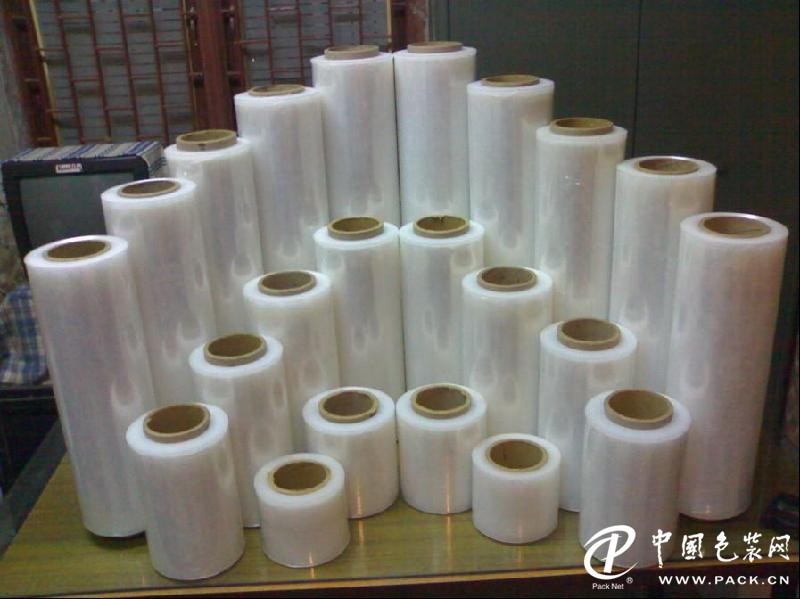
[Chinese Packaging Network News] surface three-dimensional printing (water transfer printing)
Water transfer - the use of water pressure and activator to dissolve the transfer layer on the water transfer carrier film, the basic flow is:
Film printing: printing a variety of different patterns on the polymer film;
Spray primer: Many materials must be coated with a layer of adhesive, such as metal, ceramic, etc. To transfer different patterns, different background colors must be used, such as brown, brown, khaki, etc. Basic use of white, etc.;
Extension of the membrane: Let the membrane lie flat on the surface of the water and wait for the membrane to stretch out.
Activation: The transfer film pattern is activated to a state of ink with a special solvent (activator);
Transfer: use water pressure to print the activated pattern on the printed material;
Washing: Wash the impurities remaining in the printed workpiece;
Drying: drying the printed workpiece, the temperature depends on the material's originality and melting point;
Spray paint: spray a transparent protective paint to protect the surface of the printed object;
Drying: The surface of the surface that has been sprayed is dried.
[pagebreak] There are two types of water transfer technology, one is the water mark transfer technology, and the other is the water drape transfer technology. The former mainly completes the transfer of text and photo designs, while the latter tends to complete the entire product surface. Transfer. Cubic Transfer uses an aqueous film that dissolves easily in water to carry graphics. Due to the excellent tension of the water drape film, it is easy to wrap around the surface of the product to form a graphic layer. The surface of the product has a distinctly different appearance just like the paint.
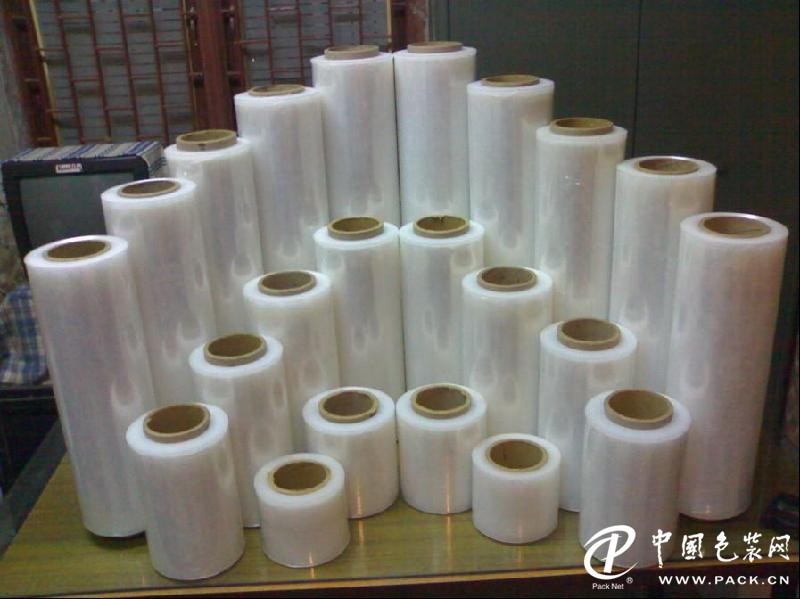
Drapery transfer technology can apply color patterns to any shape of workpiece to solve the problem of stereoscopic product printing for manufacturers. Surface coating can also be applied to the surface of the product with different textures, such as skin texture, wood grain, emerald grain and marble stone, etc., and at the same time it can also avoid the usual appearance of false printing in the surface printing. In the printing process, since the surface of the product does not need to be in contact with the printing film, damage to the product surface and its integrity can be avoided.
Brushed metal
Straight-line drawing means that a straight line is machined on the surface of the aluminum plate by mechanical rubbing. It has the dual role of brushing off the aluminum surface scratches and decorative aluminum surface. There are two kinds of continuous wire drawing and intermittent wire drawing. The continuous thread can be obtained with a scouring pad or a stainless steel brush by continuously horizontally rubbing the surface of the aluminum plate (for example, hand grinding with a device or grinding the brush with a planer on a aluminum plate).
Change the wire diameter of the stainless steel brush to obtain different thickness lines. Intermittent thread is usually processed on a brush or a rubbing machine. The principle of making: adopts two sets of differential rotating wheels that rotate in the same direction. The upper set is a roller that rotates rapidly. The lower set is a roller that rotates slowly. The aluminum or aluminum alloy plate passes through two sets of rollers and is brushed out. Delicate, intermittent lines.
Random pattern drawing is a kind of irregular matt silk pattern with no visible lines obtained by moving the aluminum plate forward and backward and left and right under the high-speed copper wire brush. This kind of processing requires high surface quality for aluminum or aluminum alloy plates.
Ripples are usually made on a brush or a scribing machine. Using the axial movement of the upper set of grinding rollers, the surface of the aluminum or aluminum alloy plate is brushed to obtain a wave pattern.
Spinning, also known as rotation, is the use of cylindrical felt or grinding stone nylon wheel mounted on the drill, with kerosene and polishing paste polishing, aluminum or aluminum alloy plate surface rotation grinding and grinding a silk pattern obtained. It is mostly used for decorative processing of round signs and small decorative dials.
The thread is a small motor equipped with a round felt on the shaft, which is fixed on the table, and is at an angle of about 60 degrees with the edge of the table, and a dragging plate with a fixed aluminum plate for pressing tea is made on the drag plate. A polyester film with straight edges is used to limit the thread race. With the rotation of the felt and the linear movement of the carriage, a thread pattern with the same width is spirally wound on the surface of the aluminum plate.
Aluminum plate engraving
Plating process
Electroplating refers to a method of surface processing in which a cation containing a metal to be plated is deposited on a surface of a base metal by electrolysis in a salt solution containing a metal to be plated, and a base metal to be plated is used as a cathode. . The coating performance is different from that of the base metal and has new features. According to the function of the coating, it can be divided into protective coating, decorative coating and other functional coatings.
Electroplating process: generally includes pre-plating pretreatment, electroplating and post-plating treatment.
Requirements for plating:
There should be good bonding between the plating and the base metal, plating and plating.
Plating should be crystal clear, flat, uniform thickness.
The coating should have a defined thickness and as few voids as possible.
Plating should have specified indicators such as brightness, hardness, and electrical conductivity.
chrome
Chromium is a light blue silver-white metal. Although the potential of the electrode is very negative, it has a strong passivation performance, and it is quickly passivated in the atmosphere, showing the properties of a precious metal, so the chrome plating of the iron part is a cathode coating. The chromium layer is stable in the atmosphere, maintains its long-term luster and is very stable in corrosive media such as alkalis, nitric acid, sulfides, carbonates, and organic acids, but is soluble in hydrochloric acids such as hydrohalic acid and hot concentrated sulfuric acid. .
The chromium layer has high hardness, good wear resistance, strong reflective ability, and good heat resistance. There was no significant change in gloss and hardness below 500 ;C; temperature greater than 500 开始C began to oxidize discoloration; greater than 700 OC began to soften.
Due to the excellent properties of the chrome plating layer, it is widely used as a protective outer layer and functional plating layer for a decorative plating system.
Copper plating
The copper-plated layer is pink, soft, has good ductility, electrical conductivity and thermal conductivity, is easy to polish, and can be decorated with bronze, copper green, black and natural colors by proper chemical treatment. Copper plating is prone to lose its luster in the air, and with the action of carbon trioxide or chloride, a layer of basic copper carbonate or copper chloride film is formed on the surface, and the sulfide will produce brown or black copper sulfide. Therefore, as The decorative copper plating layer needs to be coated with an organic coating on the surface.
Cadmium plating
Cadmium is a silver-white, shiny, soft metal that is harder than tin and softer than zinc, has good plasticity, and is easy to forge and roll. The chemical properties of cadmium are similar to those of zinc, but do not dissolve in lye, dissolve in nitric acid and ammonium nitrate, and dissolve very slowly in dilute sulfuric acid and dilute hydrochloric acid. Cadmium vapor and soluble cadmium salts are toxic and must be strictly prevented from cadmium contamination. Because cadmium contamination is very hazardous and expensive, galvanized or alloyed coatings are often used instead of cadmium plating. The types of cadmium plating solutions currently used in domestic production are: cadmium plated with ammoniacal carboxylates, cadmium plated with acidic sulphates, and cadmium plated with cyanide. There are also pyrophosphate plating cadmium, alkaline triethanolamine cadmium plating and HEDP cadmium plating.
Tin plating
Tin has a silvery white appearance with an atomic weight of 118.7, a density of 7.3 g/cm3, a melting point of 2320C, and atomic valences of divalent and tetravalent, so the electrochemical equivalents are 2.12 g/Ah and 1.107 g/Ah, respectively. Tin has the advantages of corrosion resistance, non-toxicity, easy iron welding, softness, and good ductility. Tin plating has the following features and uses:
[pagebreak] 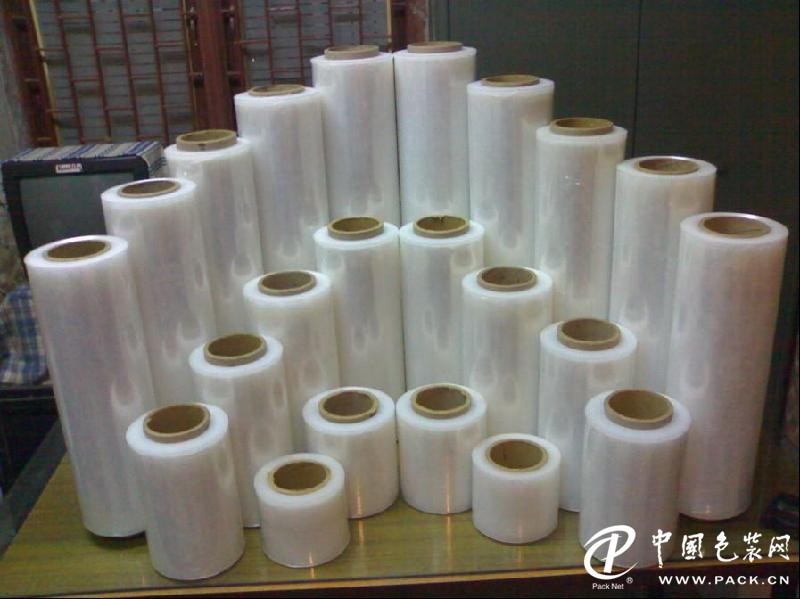
1, high chemical stability;
2. The standard potential of tin in the electrochemical sequence, ie, Fe, is a cathodic coating for steel, and can effectively protect the substrate only when the coating is not porous.
3, tin conductive, easy to weld;
4, tin began to change from -130C began to mutate, to -300C will be completely transformed into a crystalline allotrope, commonly known as "tin", at this time has completely lost the properties of tin;
5, tin and zinc, cadmium plating, in the high temperature, humidity and closed conditions can grow into whiskers, known as long hair;
6, After tin plating, it can be re-dissolved in hot oil above 2320C to obtain a glossy tin layer, which can be used as a decorative coating for daily necessities.
Plating single metal, there are lead plating, iron plating, silver plating, gold plating and so on. Electroplating alloys include: electroplated copper base alloys, electroplated zinc base alloys, electroplated cadmium bases, indium base alloys, electroplated lead bases, tin base alloys, electroplated nickel bases, cobalt base alloys, electroplated palladium nickel alloys, and the like. Composite plating includes nickel-based composite plating, zinc-based composite plating, silver-based composite plating, and diamond-inlaid composite plating.
Surface spraying (plastic parts)
The four major elements that make up a coating include:
.Resin;
Pigment
Solvent
Other additives (Additive).
The types of paint drying are as follows:
Volatile drying (evaporation and drying with thinner);
Fusion drying (molecules and molecules due to volatile phase polymerization);
Oxidative drying (unsaturated fatty acids combined with oxygen in the air);
Drying by bridging reaction (hardening by bridging agent called bridging agent);
UV hardening (unsaturated polyester additives are irradiated by UV light at a wavelength of 300-400 nm after polymerization).
Process introduction:
Coatings can be coated by dip coating, shower coating, lacquer coating, spin coating, or even vacuum coating and then cured by UV photon irradiation.
Compared with general solvent-based coatings, the characteristics of UV coatings are as follows:
Curing speed,
Normal temperature curing,
.Energy saving,
. Save floor space,
. Does not pollute the environment,
Improve product performance.
[pagebreak] Printing
Pad printing means that the substrate is an irregularly shaped surface (such as instruments, electrical parts, toys, etc.), and a copper or steel intaglio plate is used to form a hemisphere-shaped transfer head through silicone rubber, and press the plate toward the layout. Transfer the ink to the substrate to complete the transfer printing method.
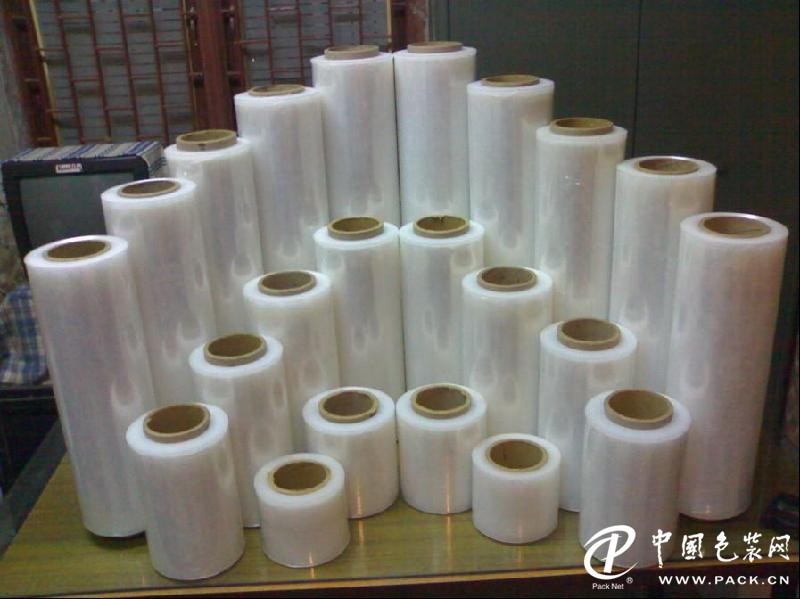
Pad printers for the industry: plastics, toys, glass, metal, electronics, sporting goods, stationery, optical industry, IC packaging industry.
Pad printer application scope: ruler, pen, ball, doll eyes, watch, camera, hair dryer shell, ceramics, medical equipment, rackets, tapes, electronic parts, IC, CPU, DRAM, computer shell, buttons, decorative signs, Brother big shell printing.
In general, the technical level of the pad printing process is not high, and it is very difficult to continue to develop in the case of high production costs in developed countries. Therefore, the pad printing industry has shifted to low-cost developing countries such as China. It is an inevitable trend. At present, apart from foreign companies that also manufacture a few high-automated pad printing lines, most companies have moved their production bases to China.
Thermal transfer
Heat transfer paper (print) is a technique that prints patterns or patterns on heat-resistant adhesive paper and prints the pattern of the ink layer onto the finished material by heating and pressing. Even for patterns of many colors, since the transfer job is just a process, the customer can shorten the operation of printing patterns and reduce the loss of materials (finished products) due to printing errors. With the use of thermal transfer film printing, multicolor patterns can be patterned at a time without trapping, and simple devices can also print realistic patterns.
Thermal transfer equipment is used to decorate aluminum-shaped materials and all kinds of metal plate materials, which can achieve the effect of wood products or marble. Thermal transfer equipment is based on the principle of thermal sublimation. It can quickly transfer the desired wood grain or marble pattern to the surface of aluminum-type powder coating and penetrate the inside of the coating in 3-5 minutes. Micron. Aluminum transfer printing process:
One is to use a film machine to roll the heat transfer film to the desired size.
The second is to use the transfer ultrasonic packaging machine that will cut the good transfer film according to the size of the workpiece and ultrasonically weld the workpiece into the bag.
The third is to insert the workpiece wrapping bag made of the transfer film on the packaging platform.
The fourth step is to place the transfer film on the heat transfer machine trolley platform. In turn, 18 aluminum materials can be placed. Connect the two ends of the aluminum material to the vacuum tap and lock it. Open the vacuum switch. The transfer film is tight at this time. Close to aluminum. The trolley automatically sends the aluminum material to the baking oven. The baking oven automatically raises the temperature by 220 degrees and keeps it warm for 3 minutes. The trolley automatically exits the baking oven.
The fifth is to loosen the vacuum tap and remove the workpiece. Sixth, remove the transfer film and check the quality of the workpiece.
Lithography thermal transfer production process, one is to use a film cutting machine to heat transfer paper roll cut into the required size. The second is to attach the thermal transfer paper film to the surface of the workpiece and put it on a flatbed hot stamping machine. The third is to push the flat plate to the heating zone of the platen heat transfer machine, press the pressure plate switch, the platen will press the thermal transfer paper tightly on the workpiece, heat and keep warm for one minute. The fourth is to raise the pressure plate, push the workpiece to the section, remove the transfer film and remove the workpiece and check it.
Thermal transfer technology is widely used in electrical appliances, daily necessities, building materials and other decorative materials. Due to its anti-corrosion, impact resistance, aging resistance, wear resistance, fire resistance, and its ability to remain in outdoor use for 15 years without discoloration, almost all products are produced using this method. For example, when you open the phone case, you can see a dense bar code label inside. Many label requirements can withstand the test of time, long-term no deformation, no fading, can not wear due to contact with the solvent, not because the temperature is higher on the deformation and discoloration, etc., it is necessary to use a special material print media and printing materials to ensure these characteristics, generally Inkjet and laser printing technologies cannot be achieved.
Sandblasting
The application of sand blasting (Sand Blasting) on ​​metal surfaces is very common. The principle is to impact the accelerated abrasive particles on the metal surface to achieve rust removal, deburring, deoxidation or surface preparation. It can change. The finish and stress state of the metal surface. Some parameters that affect sandblasting technology need attention, such as abrasive type, abrasive grain size, spray distance, spray angle, and speed. In addition to blasting, shot blasting is also a good choice.
The sandblasting process can be divided into two types: pneumatic spray gun and impeller shot blasting. The advantage of sandblasting process is that it can remove spiking, remove burrs after die casting, stamping, flame cutting and forging, for thinner workpieces and pores. The burr effect is better. It can remove the residual sand in the sand casting process, clean the rust stains of cast iron or steel, remove the oxide scale after heat treatment such as cleaning heat treatment, burning, hot forging and rolling. In addition, in coating applications, it can remove existing coatings or protective layers, providing defects such as cracks or cold lines on the castings, providing a glossy surface.
In addition to the surface stress, it can provide a consistent rough surface, oiling and spraying effects, and the metal parts such as springs and connecting rods that are subjected to high stress will be continuously beaten, and will be deformed and exhibit strengthening. This strengthening effect requires the use of circular abrasives, such as stainless steel pellets, for use in high energy shot blasting machines or special powerful blasting machines. If you want to determine the surface hardening effect of the machine, you can perform the shot blasting or sandblasting on the test workpiece, and then measure whether the deformation amount meets the requirements.
screen printing
Screen printing - The stencil with images or patterns is attached to the screen for printing.
Usually the screen is made of nylon, polyester, silk or metal mesh. When the substrate is placed directly under the stencil screen, the screen-printing ink or paint passes under the squeegee of the squeegee through the mesh in the middle of the screen and is printed on the substrate (the squeegee has manual and Automatic two).
The stencil on the screen seals a portion of the mesh aperture so that the pigment cannot pass through the screen, and only the image portion can pass through, so that only the image portion is imprinted on the substrate.
In other words, screen printing actually uses ink to permeate through the printing plate. This is why it is called silk screen printing rather than silk screen printing or silk printing because not only silk is used as a screen material, nylon, Polyester fibers, cotton, cotton, stainless steel, copper, brass, and bronze can all be used as mesh materials.
Ultrasonic welding
Ultrasonic welding is a high-tech technique for welding cooked plastic products. All kinds of cooked plastic parts can be processed by ultrasonic welding without the need of solvents, adhesives or other auxiliary products. Its advantage is to increase the multiple times productivity, reduce the cost, improve the product quality.
The principle of ultrasonic plastic welding is to generate 20KHZ (or 15KHZ) high-voltage and high-frequency signals from the generator. Through the energy exchange system, the signal is converted into high-frequency mechanical vibrations. It is applied to the workpieces of plastic products and passes through the surface of the workpiece and the intermolecular molecules. The temperature at the transfer to the interface increases due to friction, and when the temperature reaches the melting point of the workpiece itself, the working interface dissolves rapidly and fills the gap between the interfaces. When the vibration stops, the workpiece cools at a certain pressure and forms at the same time. Perfect welding.
Pressure injection
Injection molding, also known as injection molding, is an injection-molding molding method. The injection molding method has the advantages of high production speed, high efficiency, automation of operation, and ability to form parts with complex shapes. The downside is that the cost of the mold is high and the cleaning is difficult. Therefore, the small-volume products should not be molded by this method. Products molded by this method include: TV housings, semiconductor radio housings, connectors on electrical appliances, knobs, coils, gears, automotive lampshades, cups, rice bowls, soap boxes, bathtubs, sandals, and the like.
At present, injection molding is applicable to all thermoplastic plastics. The molding cycle is short, the variety of colors is many, the shape can be simple to large, the size can be from large to small, and the product size is accurate, and the product is easy to update.
Double injection molding
The two-shot molding is mainly made of two-shot molding machine with two material tubes and two sets of molds to form two-shot products through two moldings in sequence.
Compared with traditional injection molding, the two-shot co-ejection molding process has the following advantages:
The core material can use low viscosity materials to reduce the injection pressure.
From the environmental considerations, the core material can use recycled secondary materials.
According to different characteristics of use, such as the use of soft materials for thick finished leather materials, hard materials for core materials or core materials, foam plastics can be used to reduce weight.
Lower quality core materials can be used to reduce costs.
Cortical material or core material can be used with expensive and special surface properties, such as anti-electromagnetic interference, high electrical conductivity and other materials to increase product performance.
The appropriate skin material and core material can reduce the residual stress of the molded product, increase the mechanical strength or the product surface properties.
Produce products like marbled roads.
[pagebreak] From the characteristics and applications of multi-color injection molding and two-shot co-injection molding, it can be seen that there is a trend of gradually replacing the traditional injection molding process in the future. Innovative injection molding technology not only improves the precision of the injection molding process, provides difficult process technology, but also opens up the scope of the injection molding process. Innovative injection equipment and processes are sufficient to meet the increasingly diversified, high-quality, high value-added products.
Blow molding
Blow-molding is a method in which a hot parison closed in a mold is blown into a hollow product by gas pressure, or a method in which a tube parison blows without inflation into a tube film. This method is mainly used for the manufacture of various packaging containers and tubular membranes. Any melt blown material with a melt index of 0.04 to 1.12 is relatively good, such as polyethylene, polyvinyl chloride, polypropylene, polystyrene, thermoplastic polyester, polycarbonate, polyamide, cellulose acetate, and poly. Acetal resins and the like, of which polyethylene is used most.
Injection blow molding—The plastic is first made into a bottomed parison by injection molding, and then the parison is blown into a blow mold to blow a hollow product.
Extrusion blow molding—The plastic is first made into a bottomed parison by extrusion, and then the parison is blown into a blow mold and blown into a hollow product. The difference between injection blow molding and extrusion blow molding is that the method of manufacturing the parison is different, and the blow molding process is basically the same. In addition to injection molding machines and extruders, blow molding equipment is mainly used for blow molding. Blow molds are usually composed of two flaps, with a coolant channel, and a small hole on the parting surface can be inserted into a pressurized gas blowpipe.
Stretch blow molding - Stretch blow molding is a blow molding of biaxial oriented stretching by first stretching the parison longitudinally and then inflating it with compressed air to achieve transverse stretching. Stretch blow molding can greatly improve the transparency, impact strength, surface hardness and rigidity of products, and is suitable for blow molding of polypropylene and polyethylene terephthalate (PETP).
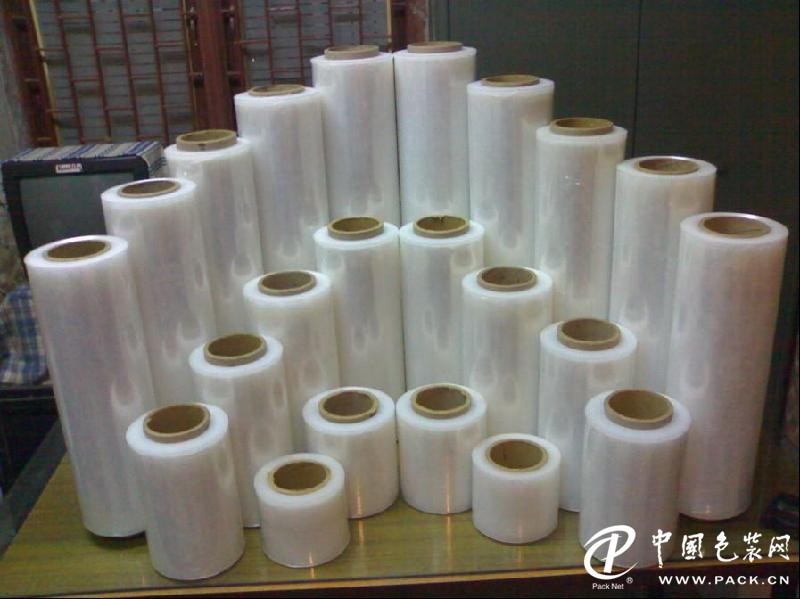
Stretch-blow molding includes: oriented parison blow-molding of an injecting parison, oriented stretch blow-molding of an extruded parison, multi-layer oriented stretch blow molding, compression-molded oriented stretch blow molding, and the like.
Blown Film Method - A method of forming a thermoplastic film. The plastic is extruded into a tube by an extrusion method, and is then continuously expanded to a tube film of a certain size by means of air blown into the tube. After cooling, it is folded and wound into a double flat film. Plastic films can be made in many ways, such as blow molding, extrusion, casting, calendering, casting, etc., but are most widely used for blow molding. This method is suitable for the production of polyethylene, polyvinyl chloride, polyamide and other films.
Stamping
Stamping is a pressure processing method that uses a mold mounted on a press to apply pressure to a material at room temperature to cause separation or plastic deformation, thereby obtaining a desired part.
Stamping features:
High stamping productivity and material utilization.
The manufactured parts have high precision, high complexity and high consistency.
. High precision molds, high technical requirements, high production costs.
Stamping materials:
The shape of the stamping material is a variety of sheets, strips, and blocks. The size of the sheet is large, and it is generally used for stamping of large parts. For small and medium-sized parts, most of them are used after being cut into strips. Banding (also known as coiling material) has a variety of widths and can be extended up to several kilometers in length. It is suitable for mass-produced automatic feeding. When the material thickness is small, it is also supplied as a band material. Blocks are used for stamping only a few steel grades and expensive non-ferrous metals.
Stamping commonly used materials are:
Ferrous metals: ordinary carbon structural steel, high-quality carbon steel, alloy structural steel, carbon tool steel, stainless steel, electrician silicon steel, and so on.
Stamping process:
Stamping processes vary depending on the shape, size, and accuracy of the parts. According to the deformation characteristics of the material, the cold stamping process can be divided into the separation process and the forming process.
Separation process - refers to the billet under the action of the punching force, after the deformation part of the stress reaches the strength limit ob, the billet breaks to produce separation. The separation process mainly includes cutting and blanking.
Forming process - refers to the billet under the impact of the pressure, the deformation part of the stress reaches the yield limit os, but does not reach the strength limit. b. Plastic deformation of the billet becomes a machining process with a certain shape, size and precision. The forming process mainly includes bending, deep drawing, flanging, spinning, and the like.
Indoor Game Equipment,Indoor Playground,Indoor Playset
Trampoline Park Co., Ltd. , http://www.nsatrampoline.com