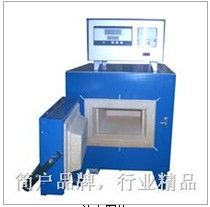
1. Working principle
The resistance furnace is an electric furnace in which Joule heat generated by current passing through a conductor is used as a heat source.
The resistance furnace uses electricity as a heat source, and converts electrical energy into heat energy through electric heating elements to heat the metal in the furnace. Resistance furnace to flame ratio, high thermal efficiency, up to 50-80â„…, easy to control thermal system, good working conditions, long furnace life, suitable for the heating of more demanding workpieces, but high power consumption costs.
According to the heat transfer method, the resistance furnace is divided into a radiation resistance furnace and a convection resistance furnace. Radiative resistance furnaces mainly use radiant heat transfer and have less convective heat transfer; convection resistance furnaces mainly use convective heat transfer, usually called air circulation resistance furnace, which is heated by hot air, and the furnace temperature is mostly below 650 ℃ .
According to the electric heating method, the resistance furnace is divided into direct heating and indirect heating.
In a direct heating resistance furnace, the current flows directly through the material. Because the electric heating power is concentrated on the material itself, the material is heated very quickly. It is suitable for processes that require rapid heating, such as forging billet heating. This resistance furnace can heat the material to a very high temperature. For example, the carbon material graphitization electric furnace can heat the material to more than 2500 â–¡. The direct heating resistance furnace can be made into a vacuum resistance heating furnace or a protective gas resistance heating furnace. In powder metallurgy, it is often used to sinter tungsten, tantalum, niobium and other products.
When using this furnace for heating, attention should be paid to: â‘ To make the material heated uniformly, the conductive cross-section and conductivity of each part of the material are required to be consistent; The contact between the power transmission electrode and the material should be good, so as not to cause the arc to burn the material, and the resistance of the power transmission bus should be small to reduce the circuit loss; â‘¢ When supplying alternating current, the short network should be reasonably configured to avoid excessive induction and power factor Too low.
Most resistance furnaces are indirect heating resistance furnaces, which are equipped with resistors specifically designed to achieve electrical-thermal transitions, called electric heaters, which transfer heat energy to the materials in the furnace. The electric furnace shell is made of steel plate, the furnace is lined with refractory materials, and the materials are placed inside. The most commonly used heaters are iron chromium aluminum heaters, nickel chromium heaters, silicon carbide rods and molybdenum disilicide rods. According to needs, the atmosphere in the furnace can be ordinary atmosphere, protective atmosphere or vacuum. The general power supply voltage is 220 volts or 380 volts. If necessary, configure an intermediate transformer with adjustable voltage. Single-phase power supply for small furnaces (<10 kW), three-phase power supply for large furnaces. For materials with a single variety and large batches, continuous furnace heating should be used. Resistance furnaces with furnace temperature below 700 â–¡, most of them are equipped with blowers to enhance heat transfer in the furnace and ensure even heating. The resistance furnace used for melting fusible metals (lead, lead-bismuth alloy, aluminum and magnesium and their alloys, etc.) can be made into a crucible furnace; or a reverberatory furnace with a molten pool, and an electric heating body is installed on the top of the furnace.
Resistance furnace-resistance furnace operation process
Second, the process before work
1. Check whether the furnace is clean and clean the sundries to ensure that the furnace is clean.
2. Check the furnace wall and the furnace floor for damage such as cracks.
3. The installation and tightening of the resistance wire and the thermocouple lead bar, check whether the instrument is normal.
4. Check whether the resistance furnace door switch is flexible.
5. After ensuring that all items are normal, start to place the workpiece.
3. Work process
1. Make sure the power is turned off when placing the workpiece.
2. Handle it gently to avoid damaging the electric heating elements, furnace floor, etc .;
3. It is strictly forbidden to put wet workpieces. The workpieces and electric heating elements heated in the furnace should be kept at a distance of 50-70mm;
4. Check all kinds of instruments during work, if there is any abnormality, timely repair.
5. When the furnace temperature is above 700 ℃, it is not allowed to open the furnace door to lower the temperature or release the furnace, so as not to shorten the furnace life due to sudden cooling.
Fourth, the process after work.
1. Power off
2. Handle the workpiece gently to ensure that the furnace body and workpiece are not damaged.
3. Reinstall the furnace and repeat the above procedure.
4. Clear the debris in the theory to ensure it is clean.
5. Pay attention to daily maintenance work.
Sports Grass the unique structure ensures the yarn has much better UP-RIGHT character which can help fibers stand up after players' stamping on fields. In addition, the structure also can make final grass feels much density.Based on advanced material technology, the fiber has great U/V resistance, longer aging performance and better feeling. Artificial grass which adopts the yarn can be widely used in soccer, futsal, rugby and other sports fields.
Sports Grass
Sports Grass,Sports Turf,Sports Lawn,Sports Artificial Lawn
Shandong Shangkun Sports Health Technology Co.,Ltd. , http://www.shangkunsports.com