Application and development of steel barrel automatic seam welding machine (1)
(Experience of developing FN250 steel drum automatic seam welding machine)
Nanjing Mining Machinery Factory Deng Jianliang
The author of this article has a certain understanding of the application of the automatic automatic seam welding machine in the barrel industry by directly participating in the digestion and absorption work, and the technical investigation and technical exchanges with the United Kingdom, the United States and Japan. And knowing for discussion.
First, the role of resistance welding machine in the development of modern barrel technology.
In order to recognize this problem, we must know the process flow of steel drum production. Figure 1 is a typical domestic and foreign steel drum production process flow chart. From the figure, from the steel plate to the finished steel drum, it takes about 20 processes, including seam welding, edge-trimming, corrugation, reinforcement, sealing technology and equipment technical conditions, which have the greatest impact on the quality of the finished steel drum. At present, many important performance indicators of steel drums have gradually been standardized internationally. For example, the International Maritime Organization has determined the full implementation of the International Maritime Dangerous Code (IMDG) in 1990 for steel drum inspection standards. The increasingly strict steel drum inspection standards have promoted the development of steel drum production technology and equipment in various countries. The key equipment of the barrels has a large update on average from 10 to -15 years to meet the needs of the new barrel making process. Among them, the development of barrel welding machines has been the fastest in the past ten years, and the foreign barrel industry has appeared. 'Arc-rolled steel drums.' This crimping process replaces the traditional rectangular double crimping process, which greatly changes the curling stress concentration of the steel drum when it falls, and the steel drum obtains better impact resistance. Performance. The main premise of the "circular curling" process improvement should first be to improve the quality of the weld.
Figure 1 Steel drum production process
Figure 2 is a section of several typical arcuate and rectangular crimps. Since the curling increases the level of overlap of the steel plates, in the mass production, the amount of overlap and overlap thickness of the barrel overlap must be controlled within 3 mm and 30%, respectively. The steel barrel automatic seam welding machine with excellent performance can be realized. In 1942, the Shanghai barrel factory first used a resistance welder. In 1957, the universal FN-150 series universal seam welder was used in the barrel factory. In 1968, the FN-150-5 seam welder, which is more suitable for the barrel industry, was introduced. In the mid-1980s, the wave of “circular curling technology†was late in China. Once it appeared, it exposed the shortcomings of the seam welder used in China's barrel industry. At the same time, China began to introduce foreign steel barrel automatic seam welding machine. In recent years, it has reached a climax. It has been speculated that the domestic barrel production plant capable of mass producing arc-rolled steel drums depends to some extent on the application of the automatic seam welding machine of the factory.
Figure 2 Arc curl and rectangular curl profile comparison
Second, the basic principle of the steel ball automatic seam welding machine work
Steel drum automatic seam welding machine belongs to the category of resistance welding machine. Resistance welding is also called contact welding. It mainly uses the principle of the thermal effect of current. Usually, the power frequency current of about 380 volts is externally connected, and a low voltage and a large current are formed in the secondary circuit of the welding machine through the welding transformer. According to Joule's law, there is resistance in the welding place:
Q=I2Rt (focus)
I—— instantaneous current value (amperes) through the weld zone
R - The total electrical resistance (ohms) of the two electrodes is a function of time.
t - the time through which the current is passed.
By selecting the welding specification, the heat generated by the resistor heats the joint of the workpiece to form a local melting (or plastic state), and a strong joint is formed under the pressure of the upper and lower electrodes. Of course, the development of resistance welding technology today, according to the form and process of the joint can be divided into several types of Figure 3. The steel drum automatic seam welding machine is actually a special seam welding machine equipped with a barrel rolling machine.
Figure 3 Classification of resistance welding
After the steel plate has been cut and treated, the steel material is automatically fed at the front of the welder. After being rounded and initially positioned, the pusher is fed between the positioning roller and the upper and lower welding wheels along the "Z" shaped guide rail. When the current of tens of thousands of amps passes, due to the high interface resistance at the lap joint of the barrel, the thermal effect causes local temperature rise. As the temperature increases, the internal resistance of the steel plate rises rapidly, and the two interact to make the welded part The metal softens into a plastic state. At this time, under the pressure of the upper and lower welding wheels, by the constant-speed linear movement, since the current of 50 Hz is periodically changed by the sine wave, a continuous welding spot is formed, so that the circle will be rounded. Between the two sides of the barrel, a joint surface having a common grain is formed. Under the further pressure of the weld bead correction roller, a uniform, tight and firm welded weld seam is formed, so that the stress in the reverse edge, the crushing, the rib and the sealing process can be withstood, and the desired process effect is obtained.
Third, the development process of resistance welding technology in the barrel industry.
Resistance welding technology has been on the lookout at the end of the last century, but it has only been used in the steel drum manufacturing industry for only about 50 years. The initial barrel welding is only a general-purpose seam welder. Due to the lack of an auxiliary mechanical system, the forming and positioning of the barrel is done separately on other equipment. Due to the lack of a mechanism for controlling the position of the weld seam during the welding process, the weld seam has a lap width of more than 10 mm. Moreover, since the thickness of the lap joint is close to twice the thickness of the steel plate, the gap between the weld seam and the bead edge occurs after the bottom or the cover is packaged, and stress concentration occurs, which becomes a weak link of the entire steel drum seal. Due to the wide lap seam of the weld, on the one hand, the current density is reduced, the thermal efficiency is not high, on the other hand, the weld seam has a burr on both sides, and when the inner and outer paint is applied, the burr is easily caused by the false coating and the exposed bottom. Corrosion occurs in advance.
In the 1960s or early 1970s, with the rapid development of the barrel industry, the quality requirements for barrel welds were getting higher and higher. Even though many factories have made many improvements to the general-purpose welders, they still cannot meet the requirements. With the development of the barrel industry in the future, the United States Niu Tong Company and the British Federal Welding Machine Company have successively developed a steel barrel automatic seam welding machine. The welder consists of two parts, forming and welding, and adds "Z" guide rail, leaky positioning roller and weld correction mechanism, so that the barrel weld overlap is controlled within 3 mm. The welder has a rated power of 250 to 400? and a welding speed of 12 m/min, which is equivalent to welding 720 200 litre drums per hour.
With the development of resistance welding technology, the American Karundo Company began trial production of the automatic high-speed welding machine for steel drums with secondary rectification and power supply in the late 1970s. The usual resistance welding machine is generally powered by a commercial frequency AC power supply. The reactive power consumed by the welding circuit impedance and the power consumed by the secondary winding of the transformer due to heat generation account for about 60% of the input power. In order to solve these problems, in recent years, countries have focused on the development of secondary rectification welders in resistance welding technology. In contrast, this welder greatly increases the efficiency of welding and reduces the amount of electricity consumed by each barrel. Since there is almost no consumption of reactive power, the power factor of the welding circuit is as high as 95%. In addition, the welder does not have to consider the influence of the barrel on the impedance during the welding process. Figure 4 shows the current changes in the AC and secondary rectification welders when welding the cylindrical workpiece. In the circuit of the figure, the arm spacing is 200 mm, the wall thickness of the barrel is 6 = 1+1 mm, and the length is about 1 meter. This holdability allows the welder to achieve a more stable current and heat field, ensuring high quality barrel welds. In the design of the welder circuit, since the secondary rectifying welder has almost no requirements on the loop inductance, it can be more compact structure design without being affected by the geometry and material. Due to these advantages of the secondary rectification automatic seam welding machine, the MOdeL 1424-3 automatic welding machine recently manufactured by Karendo Company of the United States has a rated input power of 140 KVA and a welding speed of up to 20 m/min. That is, it can weld 1200 barrels of 200 liter steel drum per hour. It is the world's fastest and most efficient steel drum automatic welding machine.
Figure 4 Current changes when welding a barrel-shaped workpiece
Self Adhesive Whiteboard
Self adhesive whiteboard is a kind of Portable Whiteboard with adhesive, easy cut,bent,twisted,coiled,or can machined into almost any shape. Due to strong adhesive,the Whiteboard Sticker easy to install and won't fall off easily. No need to drill holes in your wall and can be install any smooth surface like desk,cabinet and so on.
The steel sheeting of whiteboard has a certain thickness so that it does install with no wrinkles and no bubbles. At the same time,big size is the feature of soft whiteboard and this whiteboard sticker is consequently becoming increasing popular for the use as Whiteboard Wallpaper.
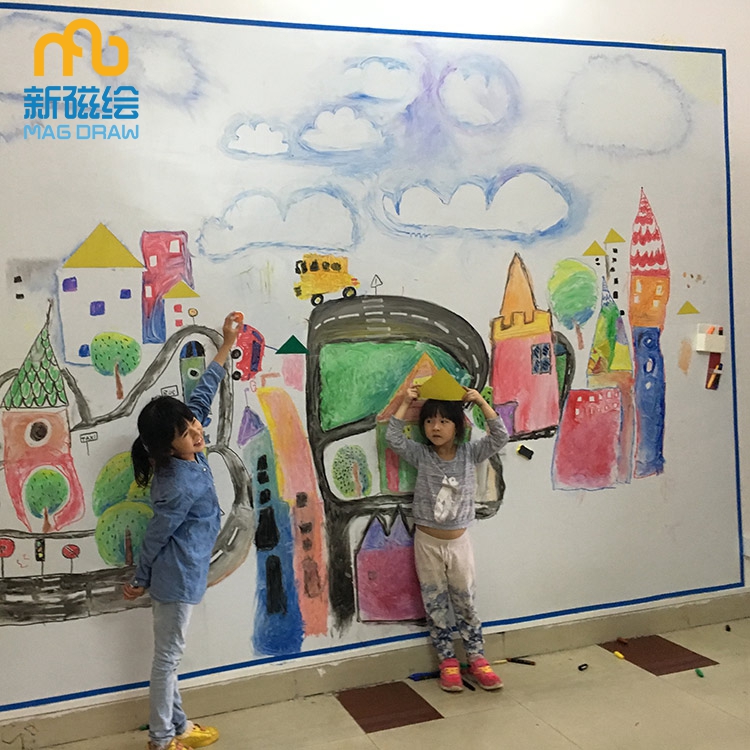
Self Adhesive Whiteboard
Self Adhesive Whiteboard,Adhesive Whiteboard Roll,Whiteboard Sticker,Whiteboard Wallpaper
Guangzhou New Magnetics Technology Co.,Ltd , http://www.softwhiteboard.com